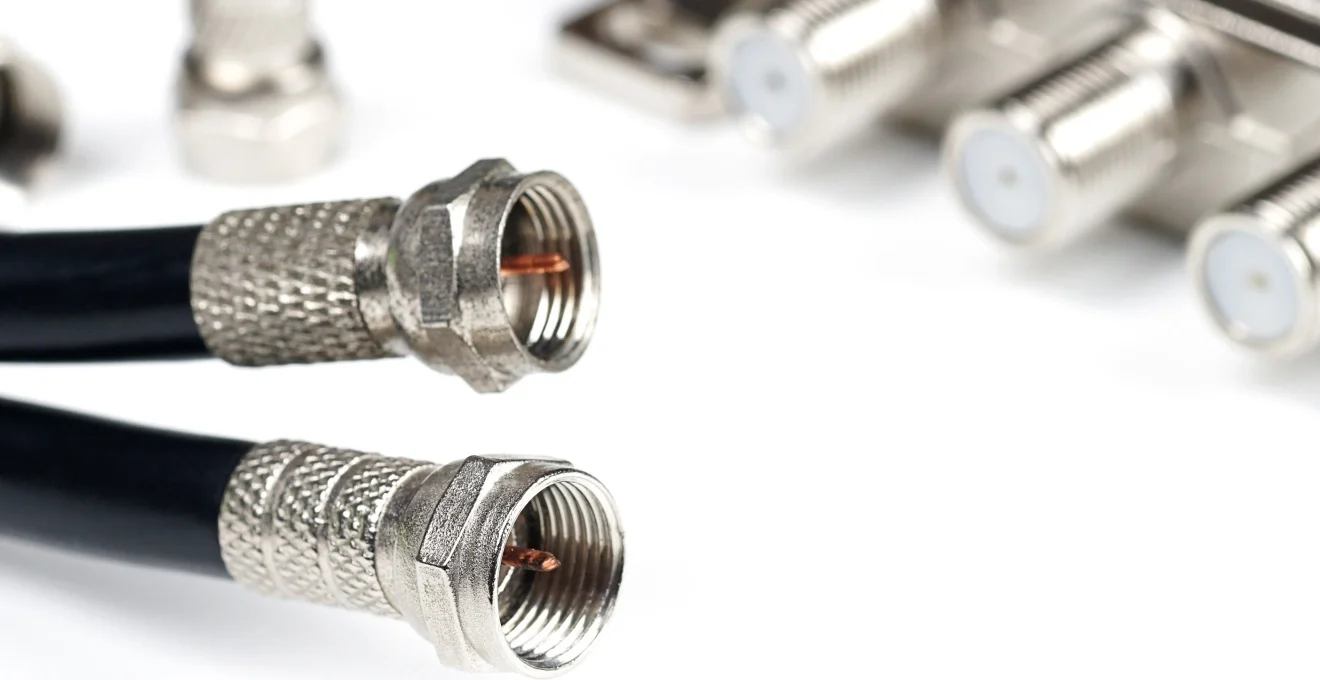
Electrical connectors are the unsung heroes of modern electronics, playing a crucial role in powering and connecting our devices. As technology advances at breakneck speed, the demand for more sophisticated, compact, and reliable connectors continues to grow. From smartphones to industrial machinery, these essential components are undergoing a transformation to meet the evolving needs of various industries.
Miniaturization trends in modern connector design
One of the most significant trends in electrical connector design is the push towards miniaturization. As devices become smaller and more portable, the need for compact connectors has never been greater. This trend is particularly evident in consumer electronics, where space is at a premium.
Manufacturers are developing connectors with smaller form factors without compromising on performance or reliability. This miniaturization effort involves innovative design techniques and the use of advanced materials. For instance, micro-miniature connectors are now capable of handling high-speed data transmission while occupying minimal space on a circuit board.
The challenge lies in maintaining the structural integrity and electrical performance of these smaller connectors. Engineers are employing sophisticated computer-aided design (CAD) tools to optimize connector geometries and ensure proper signal integrity. Additionally, advancements in manufacturing processes, such as micro-molding and high-precision machining, are making it possible to produce these intricate components at scale.
As a result of these miniaturization efforts, we're seeing the emergence of ultra-compact connectors that are revolutionizing product design across various industries. From wearable technology to aerospace applications, these miniature connectors are enabling the creation of sleeker, lighter, and more efficient devices.
For those interested in learning more about the various types of electronic connectors and their applications, icape-group.com offers a comprehensive guide that covers everything from basic designs to advanced features.
Advanced materials revolutionizing electrical connectors
The quest for improved connector performance has led to significant advancements in materials science. Traditional materials like copper and brass are being supplemented or replaced by innovative alternatives that offer superior electrical and mechanical properties. These new materials are enabling connectors to meet the demanding requirements of modern applications.
Nanotechnology-enhanced conductive polymers
One of the most exciting developments in connector materials is the use of nanotechnology-enhanced conductive polymers. These materials combine the flexibility and lightweight properties of plastics with the conductivity of metals. By incorporating nanoparticles or nanotubes into polymer matrices, researchers have created materials that can conduct electricity efficiently while remaining lightweight and resistant to corrosion.
These conductive polymers are particularly useful in applications where weight is a critical factor, such as in aerospace or portable electronics. They also offer the potential for creating flexible connectors that can withstand repeated bending and flexing without losing their electrical properties.
High-temperature ceramic insulators for extreme environments
In industries such as automotive and aerospace, connectors often need to operate in extreme temperature conditions. Traditional plastic insulators may not be suitable for these environments. To address this challenge, manufacturers are turning to high-temperature ceramic materials.
Ceramics like aluminum nitride and boron nitride offer excellent thermal stability and electrical insulation properties. These materials can withstand temperatures well above 200°C, making them ideal for use in engine compartments or other high-heat applications. The integration of ceramic insulators in connector design has significantly expanded the operating range of electrical connectors, enabling their use in previously challenging environments.
Carbon nanotube integration in contact surfaces
Carbon nanotubes (CNTs) are revolutionizing the way we think about electrical contacts in connectors. These microscopic structures offer exceptional electrical and thermal conductivity, along with remarkable strength. By incorporating CNTs into contact surfaces, connector manufacturers are creating more reliable and efficient connections.
The use of CNTs can reduce contact resistance, improve current-carrying capacity, and enhance the overall durability of the connector. This technology is particularly promising for high-power applications where traditional contact materials may struggle to meet performance requirements.
Self-healing materials for enhanced durability
One of the most intriguing developments in connector materials is the emergence of self-healing technologies. These materials have the ability to repair minor damage automatically, potentially extending the lifespan of connectors and reducing maintenance requirements.
Self-healing polymers, for example, contain microcapsules filled with healing agents. When a crack or scratch occurs, these capsules rupture, releasing the healing agent and repairing the damage. This technology could be particularly valuable in connectors used in vibration-prone environments or those subject to frequent mating cycles.
Smart connectors: integrating iot and sensing technologies
The Internet of Things (IoT) revolution is transforming the way we interact with devices and systems. Electrical connectors are not immune to this trend, and we're seeing the emergence of "smart connectors" that incorporate sensing and communication capabilities.
Embedded RFID systems for connector identification
Radio-Frequency Identification (RFID) technology is being integrated into connectors to enable automated identification and tracking. This feature is particularly useful in complex systems where multiple connectors are present. RFID-enabled connectors can provide information about their specifications, installation date, and maintenance history, simplifying inventory management and troubleshooting processes.
Real-time temperature and humidity monitoring
Smart connectors equipped with temperature and humidity sensors can provide real-time data on environmental conditions. This information is crucial for applications where these factors can affect performance or safety. For instance, in data centers, where overheating can lead to system failures, connectors with integrated temperature monitoring can provide early warnings of potential issues.
Predictive maintenance through data analytics
By collecting and analyzing data from smart connectors, it's possible to implement predictive maintenance strategies. Connectors can monitor their own performance, detecting signs of wear or deterioration before a failure occurs. This proactive approach can significantly reduce downtime and maintenance costs in industrial settings.
Wireless power transfer in smart connectors
The integration of wireless power transfer technology into connectors is opening up new possibilities for device charging and power distribution. These smart connectors can eliminate the need for physical contact in some applications, reducing wear and tear and improving reliability.
High-speed data transmission advancements
As our world becomes increasingly data-driven, the demand for connectors capable of handling high-speed data transmission continues to grow. This trend is particularly evident in telecommunications, data centers, and consumer electronics sectors.
Engineers are developing connectors that can support data rates of 100 Gbps and beyond. These high-speed connectors often employ advanced shielding techniques to minimize electromagnetic interference (EMI) and maintain signal integrity. Materials like high-performance polymers and advanced alloys are being used to create connector structures that can handle the increased frequencies associated with high-speed data transmission.
One notable development in this area is the use of photonic connectors, which utilize light instead of electrical signals to transmit data. These connectors have the potential to dramatically increase data transfer speeds while reducing power consumption and heat generation.
Another innovation in high-speed connectivity is the development of active optical cables (AOCs). These cables integrate optical transceivers directly into the connector, converting electrical signals to optical signals and vice versa. AOCs can transmit data over longer distances with less signal degradation compared to traditional copper cables.
Environmental sustainability in connector manufacturing
As environmental concerns take center stage globally, the electrical connector industry is also focusing on developing more sustainable products and manufacturing processes. This shift towards sustainability is not just about regulatory compliance; it's becoming a key differentiator in the market.
Biodegradable connector components
Research is underway to develop biodegradable materials for use in connector components. While these materials may not be suitable for all applications, they could significantly reduce the environmental impact of connectors used in short-term or disposable products. For example, biodegradable plastics derived from renewable resources are being explored for use in connector housings.
Energy-efficient production processes
Manufacturers are implementing energy-efficient production processes to reduce their carbon footprint. This includes the use of renewable energy sources, optimizing manufacturing lines for energy conservation, and implementing waste heat recovery systems. Advanced manufacturing techniques like 3D printing are also being explored for their potential to reduce material waste and energy consumption in connector production.
Recycling and circular economy initiatives
The concept of a circular economy is gaining traction in the connector industry. Manufacturers are designing connectors with recyclability in mind, using materials that can be easily separated and recycled at the end of the product's life. Some companies are even implementing take-back programs to ensure proper recycling of their products.
Additionally, there's a growing focus on using recycled materials in connector production. For instance, some manufacturers are incorporating recycled metals into their connector contacts, reducing the demand for virgin materials.
Ruggedization techniques for harsh industrial environments
In industrial settings, connectors often need to withstand extreme conditions, including high temperatures, vibrations, and exposure to corrosive substances. The ruggedization of connectors is a critical area of innovation, ensuring reliable performance in challenging environments.
One approach to ruggedization is the use of hermetic sealing techniques. These methods create an airtight and watertight seal around the connector, protecting it from moisture, dust, and other contaminants. Advanced sealing materials, such as fluorosilicone elastomers, are being used to create flexible yet durable seals that can withstand a wide range of temperatures and chemicals.
Another important aspect of ruggedization is shock and vibration resistance. Manufacturers are employing various design strategies to enhance the mechanical stability of connectors. This includes the use of robust locking mechanisms, reinforced housing designs, and flexible contact systems that can absorb vibrations without losing electrical connectivity.
Corrosion resistance is also a key focus in ruggedized connector design. Advanced plating techniques, such as nickel-PTFE composite coatings, are being used to protect connector contacts from corrosive environments. These coatings not only prevent corrosion but also provide improved wear resistance and lubricity, which can be beneficial in applications with frequent mating cycles.
The development of modular connector systems is another trend in ruggedization. These systems allow for easy replacement of damaged components without the need to replace the entire connector assembly. This modularity not only improves maintainability but also extends the overall lifespan of the connector system in harsh environments.
As industrial automation continues to advance, the need for connectors that can withstand harsh conditions while delivering high-speed data and power transmission is becoming increasingly critical. Manufacturers are rising to this challenge by combining ruggedization techniques with advanced materials and smart technologies to create connectors that are truly built for the industrial Internet of Things (IIoT) era.
The field of electrical connector design is undergoing a remarkable transformation, driven by the demands of emerging technologies and the need for more efficient, durable, and sustainable solutions. From miniaturization and advanced materials to smart technologies and ruggedization, these innovations are shaping the future of connectivity across various industries. As we continue to push the boundaries of what's possible, electrical connectors will undoubtedly play a crucial role in enabling the next generation of electronic devices and systems.